ACCORD – Transferprojekt zur Industrialisierung der 3D-Skelett-Wickeltechnik (3DSW)
Die 3D-Skelett-Wickeltechnik (3DSW) ist ein roboterbasiertes 3D-Faserwickelverfahren zur Herstellung kontinuierlich faserverstärkter Thermoplast-Skelettstrukturen. Seine wissenschaftlichen Grundlagen wurden und werden am Fraunhofer Institut für Chemische Technologie ICT in Pfinztal erarbeitet. Ziel der 3DSW ist es, Versteifungsskelette effizient und funktionsoptimiert in hochbelastete Bereiche von Polymer-Formteilen zu integrieren.

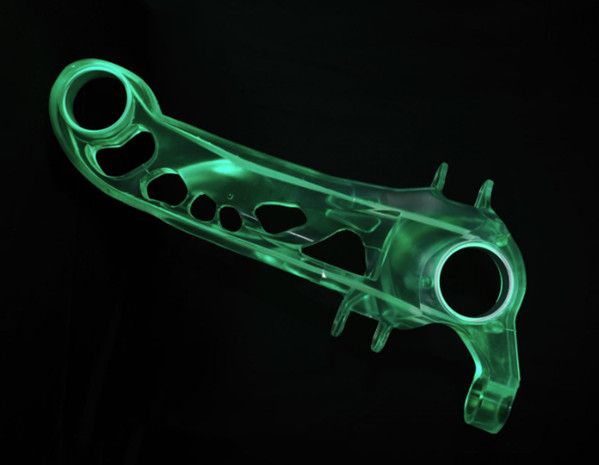
Zur Herstellung der »Faserskelette« werden thermoplastisch imprägnierte Verstärkungsfasern (zum Beispiel Glas-, Natur- oder Kohlenstofffasern) auf Basis von Hybridgarnen Roboter-basiert auf Wickelwerkzeuge oder Kerne gewickelt. Die Freiheitsgrade eines 6-Achsen-Industrieroboters und die garnbasierten Faserhalbzeuge erlauben eine präzise physische Nachbildung topologieoptimierter Strukturen mit lastpfadoptimierter Faserausrichtung. Die Faserskelette können zur lokalen Verstärkung verschiedener Bauteiltypen eingesetzt werden, beispielsweise innerhalb von Spritzgieß-Formteilen oder als externe Verstärkung additiv gefertigter Strukturen. Darüber hinaus ist es möglich, 3DSW-Faserskelettstrukturen ohne angrenzende Strukturen als Extremleichtbaukomponenten einzusetzen (Skelettbauteile).
Im Rahmen des ACCORD-Projekts ist es in Zusammenarbeit mit der Fritz Automation GmbH gelungen, die – bislang lediglich im Labormaßstab praktizierte – Fertigungstechnologie in einen industrie- und großserientauglichen Maßstab zu überführen. Zunächst waren hierbei Automatisierungslücken zu schließen, die im Labor durch manuelle Eingriffe überbrückt wurden. Die im Projekt errichtete Fertigungszelle ermöglicht die vollautomatische Ausführung des kompletten 3DSW-Fertigungsprozesses.
Im Hinblick auf den industriellen Einsatz überzeugt neben der CE-Zertifizierung der errichteten Anlage insbesondere die implementierte Datenaufzeichnung. Die Echtzeitmessung der Abzugsgeschwindigkeit und der Materialtemperatur an verschiedenen Punkten ermöglicht eine effektive Prozess- und Qualitätsüberwachung.
Die beschriebene Anlagentechnik hebt die 3DSW und das thermoplastische, kernlose 3D-Faserwickeln im Allgemeinen auf eine neue Stufe der Automatisierbarkeit. Die konsequente Automatisierung des gesamten Fertigungszyklus einschließlich vermeintlicher Details wie der Bereitstellung temperierter Inserts und der Abfrage der Garntemperatur zu Beginn des Wickelvorgangs ist Grundlage für eine erfolgreiche Serienfertigung mit reproduzierbar hoher Qualität.
Als weitere Innovation ist insbesondere die Mikrowellenheizung anzuführen. Sie ist, zusätzlich zu den Infrarotstrahlern und der beheizten Konsolidierdüse (Kontakterwärmung) als dritte Heiztechnologie verfügbar. Verglichen mit den anderen beiden Technologien zeichnet sie sich durch ein sehr schnelles Ansprechverhalten bei Sollwert-Änderungen aus. Sie ist ein Schlüsselfaktor, um auch komplexe Faserskelette, die sich nicht mit konstanter Abzugsgeschwindigkeit wickeln lassen, bei gleichbleibend hoher Faserimprägnierungsqualität umzusetzen. Hierzu wird die Leistungsaufnahme der Mikrowellenheizung in Echtzeit an die gemessene Abzugsgeschwindigkeit angepasst.
Am Beispiel des betrachteten Demonstrators konnte das Leichtbaupotenzial der Technologie nachgewiesen werden. Eine Demonstrator-Komponente, die im ACCORD-Projekt von der Simutence GmbH entwickelt und von der Fritz Automation GmbH gemeinsam mit dem Fraunhofer ICT prototypisch gefertigt wurde, ist ein Hinterachs-Längslenker für ein Pkw-Modell der Marke Hyundai, einem assoziierten Partner des Projekts. Laut Simulationsergebnissen der Simutence GmbH konnte die Bauteilmasse gegenüber dem Originalbauteil aus Stahlblech um rund 37 Prozent reduziert werden – bei vergleichbarer Bauteilsteifigkeit und höherer Belastbarkeit. Der Demonstrator ist als skelett-verstärktes Formteil konzipiert, wobei das Faserskelett aus kontinuierlich glasfaserverstärktem PA6 besteht und die Einbettung aus Kurzglasfaser-verstärktem PA6.
Zentrale mechanische Vorzüge der 3DSW sind:
- Verwendung höchstfester Materialien (kontinuierliche Faserverstärkung)
- minimalistischer Materialeinsatz (im Sinne der additiven Fertigung wird nur dort Material platziert, wo es benötigt wird)
- formschlüssige Lastübertragung durch Umwickeln von Lasteinleitungselementen.